I actually did this mod on my C70 back in July, but am just getting around to posting about it here.
I have a system I use for testing and diagnostics that was in an old crappy generic tower and decided to get a
Corsair C70 replacement case for a couple of reasons....
For practical reasons, I liked the quick release side panel latches that make getting into the case very quick and
easy. The machine is used for testing hardware, imaging drives, etc. so it's nice to have those latches.
It also has strong sturdy handles on the top of the tower that make picking up the case to move it nice and easy.
Something I do a lot of in my home office, working as an independent IT consultant.
The case is nice and large, plenty of room inside, and it looks cool. So plenty of reason for me to snag one when
it went on sale. Price matched Amazon at Microcenter.
So I moved the hardware from the old case to the C70 and was happy with it for 4-5 months. I knew even when I bought
it that I was going to change that stock plexi window side panel with the fan mounts in it. It looks bad, and you'll see
that as a complaint from buyers and online reviews.
I decided to replace the plexi window with a flat black aluminum panel. I also wanted to seal up the open top vents on
the tower that let dust and debris fall inside the case.
So I ordered a flat black painted aluminum panel from Amazon. The description was "Matte Black / White Painted
Aluminum Sheet .040" x 12" x 24"". The 12" side was just barely wide enough to cover the side panel window and the
top vent. The 24" side gave me plenty of material to cut the two pieces I needed with a small scrap left over. I bought
some bags of rubber grommets from ACE Hardware to mount the new aluminum panel. I took one of the window trim
pieces with me to the hardware store to make sure I got the right size grommets. From memory I think they were the
1/4" size and were in plastic bags of 6 in the electrical section, not where they have the millions of parts in the drawers.
The grommets fit on the posts and are just a hair taller than the posts when installed. The screws will compress them
slightly when screwed down (don't over tighten).
I'm not an especially skilled guy with regard to shop skills but I got through it ok and it looks like a factory job. I used
a brand new set of sharp tin snips to cut the aluminum by hand and a cordless drill for the mounting holes.
This guy has smoked plexi replacement windows for the C70, but they were never in stock, so I just decided to do
my own thing and went with the flat black aluminum. The video is still good to see how the swap is done.
If anybody is interested, I can post a few more details about cutting the aluminum and getting it installed.
Pics:
.
ETA: With the military theme of the case, I call this "buttoning up" the case. Similar to the way a tank
commander would order "button up" (close hatches and vents) before going into battle.
.
I have a system I use for testing and diagnostics that was in an old crappy generic tower and decided to get a
Corsair C70 replacement case for a couple of reasons....
For practical reasons, I liked the quick release side panel latches that make getting into the case very quick and
easy. The machine is used for testing hardware, imaging drives, etc. so it's nice to have those latches.
It also has strong sturdy handles on the top of the tower that make picking up the case to move it nice and easy.
Something I do a lot of in my home office, working as an independent IT consultant.
The case is nice and large, plenty of room inside, and it looks cool. So plenty of reason for me to snag one when
it went on sale. Price matched Amazon at Microcenter.
So I moved the hardware from the old case to the C70 and was happy with it for 4-5 months. I knew even when I bought
it that I was going to change that stock plexi window side panel with the fan mounts in it. It looks bad, and you'll see
that as a complaint from buyers and online reviews.
I decided to replace the plexi window with a flat black aluminum panel. I also wanted to seal up the open top vents on
the tower that let dust and debris fall inside the case.
So I ordered a flat black painted aluminum panel from Amazon. The description was "Matte Black / White Painted
Aluminum Sheet .040" x 12" x 24"". The 12" side was just barely wide enough to cover the side panel window and the
top vent. The 24" side gave me plenty of material to cut the two pieces I needed with a small scrap left over. I bought
some bags of rubber grommets from ACE Hardware to mount the new aluminum panel. I took one of the window trim
pieces with me to the hardware store to make sure I got the right size grommets. From memory I think they were the
1/4" size and were in plastic bags of 6 in the electrical section, not where they have the millions of parts in the drawers.
The grommets fit on the posts and are just a hair taller than the posts when installed. The screws will compress them
slightly when screwed down (don't over tighten).
I'm not an especially skilled guy with regard to shop skills but I got through it ok and it looks like a factory job. I used
a brand new set of sharp tin snips to cut the aluminum by hand and a cordless drill for the mounting holes.
This guy has smoked plexi replacement windows for the C70, but they were never in stock, so I just decided to do
my own thing and went with the flat black aluminum. The video is still good to see how the swap is done.
If anybody is interested, I can post a few more details about cutting the aluminum and getting it installed.
Pics:
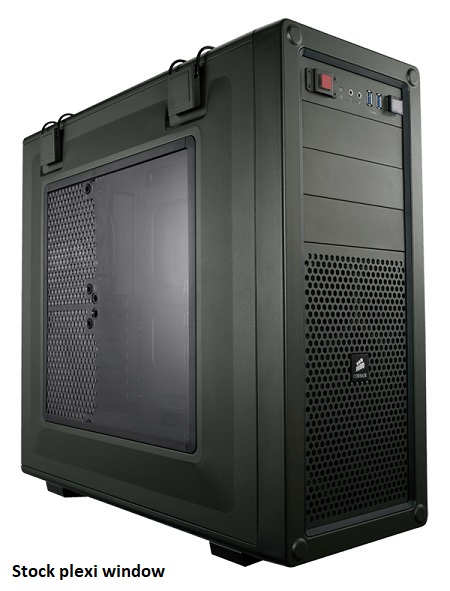
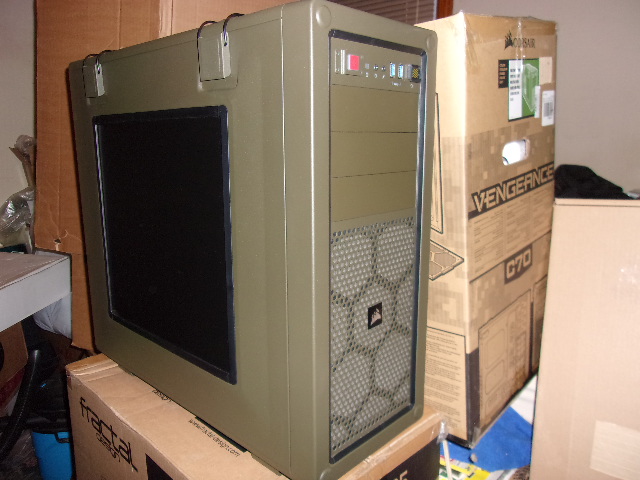
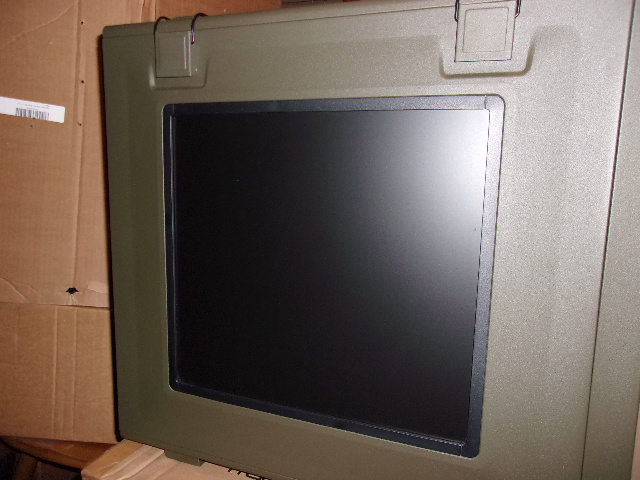
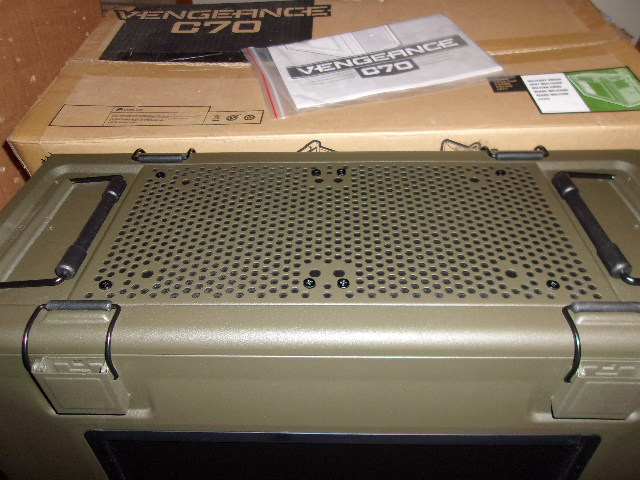
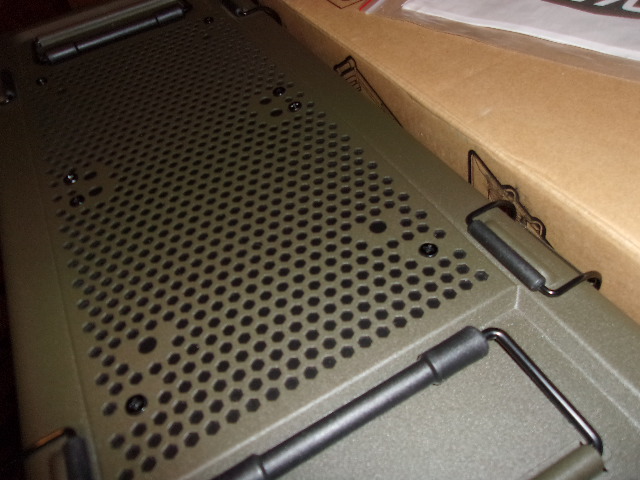
.
ETA: With the military theme of the case, I call this "buttoning up" the case. Similar to the way a tank
commander would order "button up" (close hatches and vents) before going into battle.
.
Last edited: