UPDATE!!!!!!!!!!!!!!!!!!!!!!!!!!!!!!!
Finally I have gotten a chance after a long long while to get some new pics!!!!!!
Here are some new pics regarding:
1. Carbon fiber vinyl
2. Installing the carbon fiber vinyl on many components of the case
3. Wiring plate (tell me what you think of it)
4. New Brace system using 1" x 1" aluminum tubing welded
5. All water blocks installed and final tubing assembly done!
6. G15 Keyboard wrapped in carbon fiber vinyl
Ok here we go, there are 51 pictures
Enjoy
OK finally my G15 keyboard wrapped in carbon fiber vinyl.
You will notice that i didnt have the G15 name on the right side cut out yet, i had to get a new blade for my xacto knife to cut it out.
let me know what you think!!
If anyone wants to get this mod done, let me know, we can set something up!
Finally I have gotten a chance after a long long while to get some new pics!!!!!!
Here are some new pics regarding:
1. Carbon fiber vinyl
2. Installing the carbon fiber vinyl on many components of the case
3. Wiring plate (tell me what you think of it)
4. New Brace system using 1" x 1" aluminum tubing welded
5. All water blocks installed and final tubing assembly done!
6. G15 Keyboard wrapped in carbon fiber vinyl
Ok here we go, there are 51 pictures
Enjoy
OK finally my G15 keyboard wrapped in carbon fiber vinyl.
You will notice that i didnt have the G15 name on the right side cut out yet, i had to get a new blade for my xacto knife to cut it out.
let me know what you think!!
If anyone wants to get this mod done, let me know, we can set something up!

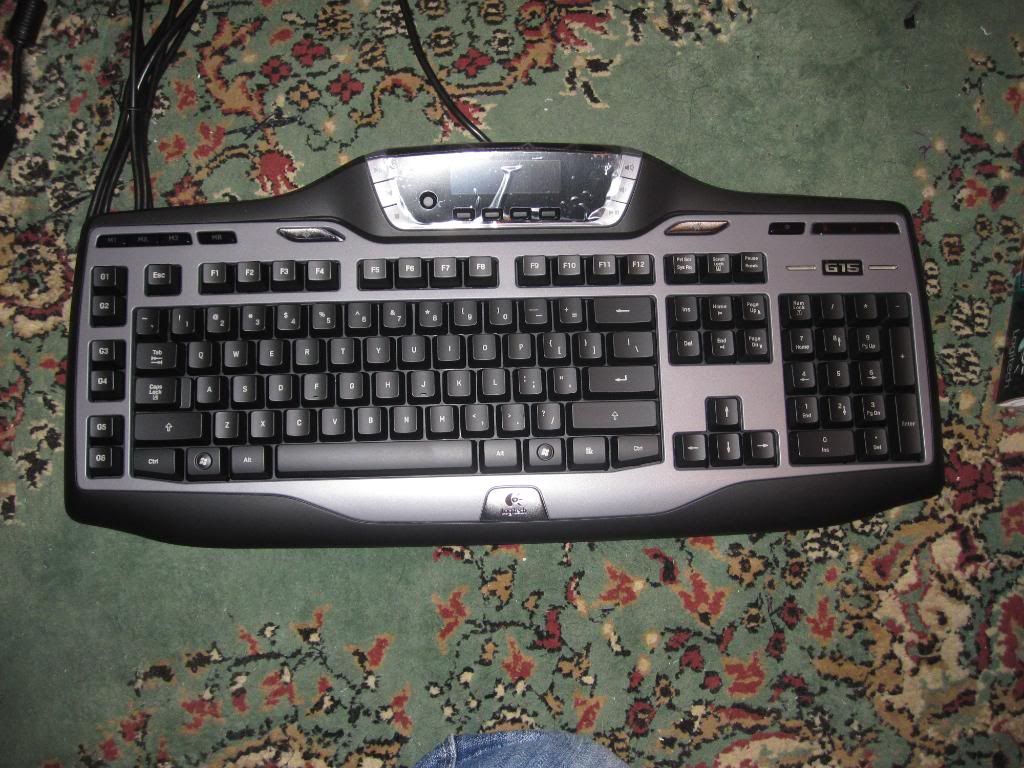
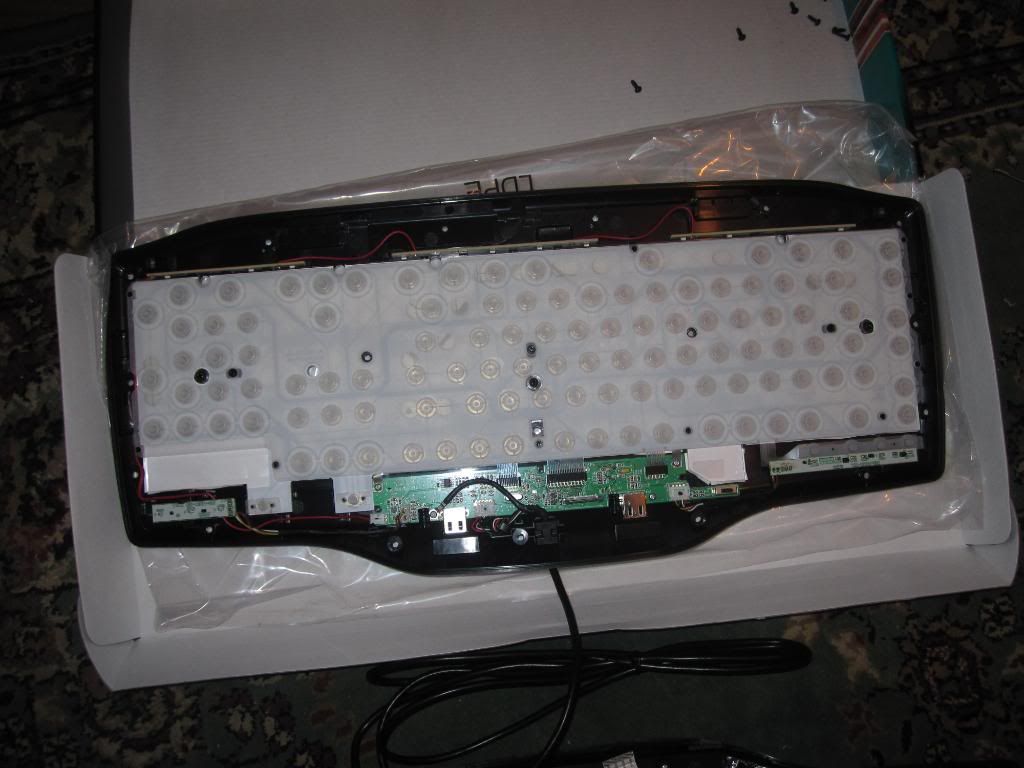
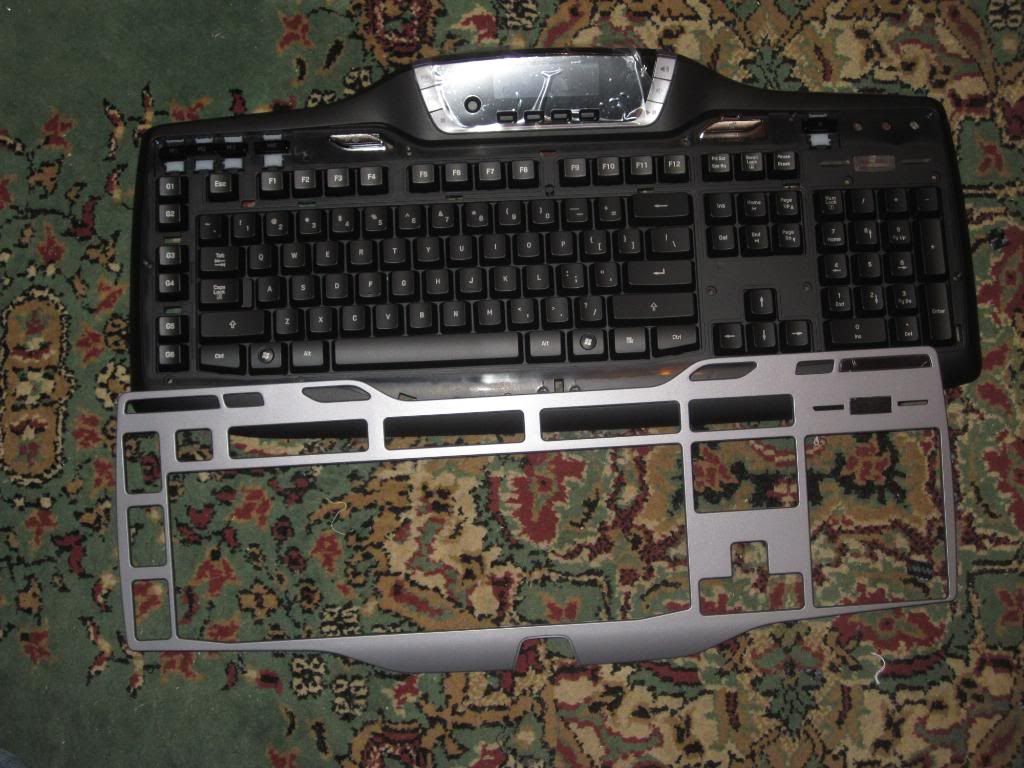
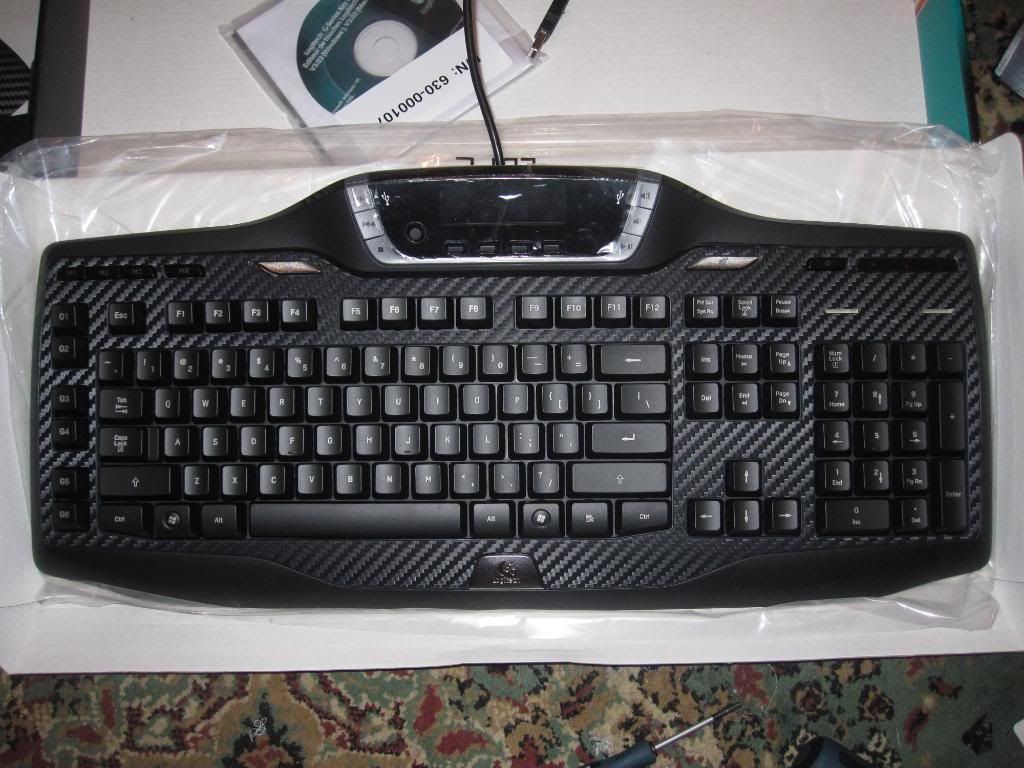